Textile Effluent Treatment Technologies
Textile Industry
Textiles, materials, and clothes are all part of the textile sector, which includes exploration, creation, innovation, production, and sales. Textiles and garments were prepared in the home by persons for their use pre-industrial. They were frequently marketed on a low scale. With the creation of the invention in 1733, the spinning jenny in 1764, and the power loom in 1784, the textile industry was born. Then widespread use of materials and garments started. When James Watt refined his steam turbine in 1775, Eli Whitney developed a cotton gin in 1792, and Elias Howe innovated a sewing machine in 1846, they all greatly contributed to the textile company’s prosperity.
A textile industry consists of the following departments
- Spinning
- Fabric manufacturing department
- Garments manufacturing
Sheets, comforters, cushions, and bathrobes are made by various textile firms. The textile business also includes the inflow and outflow of materials and clothing. In addition, buyers for clothes design and production frequently travel the globe in search of the proper fabric for their designs.
Textile manufacturing operations, from fibre production to final fabric finishing, significantly impact all environmental realms, including air, water, and soil. As a result, the textile industry has implemented several public-private collaboration projects to improve the environmentally friendly character of textile processing. Water and chemicals are present throughout the textile processing chain. Fiber processing and production, such as sizing, desizing, scouring, bleaching, mercerization, dyeing, printing, and finishing, are noted for their high water, chemical, and energy consumption.
Characteristics Of Textile Effluents Industry
The textile industry is one of the most important parts of any industrial sector but this industry is also a source of waste that destroys our environment. We classified textile effluents released from textile industries into four different types. Each category has different characteristics and required different preventive measures and methods to solve them. Such four categories are discussed here:
- Hard to treat Waste
In this category we generally deal with, we generally deal with persistent waste products or interact with the functioning of treatment and disposal share similar characteristics. The common contributors of wastes consist of color, metals, phenolic compounds, some surfactants, poisonous organic matter, chemicals, and phosphates, which are non-biodegradable organic or inorganic components. - Lethal or Poisonous Wastes
These wastes are a subcategory of garbage that is refractory to treatment. They are, however, classified as a specific class due to their significant environmental impact. Metals, chlorine and their solvents, non-biodegradable or unstable organic compounds are examples of harmful toxic wastes in textiles. Non-process operations, such as apparatus washing, are common uses for many of these materials. - High Capacity Waste
For fabric production operations, vast quantities of waste might be a challenge. The following are the most common large-volume wastes:
-
-
- A huge volume of wastewater
- Wash alkali wastes from preparatory methods as well as liquid from preparatory and continuously coloring processes.
- Large amounts of salt, acid, or alkaline in industrial dye effluent
- These pollutants can occasionally be lowered by recycling or reuse, as well as changes to manufacturing techniques.
-
- Dispersible waste
The methods listed below in the garment industry generate high dispersible waste:
-
-
- Continuous-flow effluent drain (e.g. preparatory, dyeing, printing, and finishing)
- Paste & print (printing screen, squeeze, and drum cleaning)
- Sticky stuff is a type of fluff (preparatory, dyeing, and washing operations
- Bubbles formed during the surface coating
- Liquids discharged throughout appliance washing
- Liquid extraction has been produced in still tops (dry cleaning operation)
- Wasted handling batch dumps (finishing mixes)
-
The pollutants discharged from each step of the textile industry are shown in this diagram:

TREATMENT TECHNOLOGIES
We have three treatment technologies for treating textile effluents:
- Primary Treatment
- Secondary Treatment
- Tertiary Treatment
- PRIMARY TREATMENT The first step to Effluent Recycling Systems, is to eliminate as many textile effluents and suspended particles as feasible after removing coarse solids, abrasive materials, and an excessive amount of oils. This process is intended to reduce the waste water’s intensity while also facilitating secondary treatment.
MECHANICAL FLOCCULATION AND CHEMICAL COAGULATION
They are used to remove finely dispersed suspended particles and colloidal particles that are too small to be removed by gravity alone. Mechanical flocculation and chemical coagulation are used in certain situations. The textile contaminated water is circulated through a tank with mild agitation; the finely separated suspended materials agglomerate into large particles and settle out via mechanical flocculation. There is also specialized equipment, such as a clariflocculator, which is a sedimentation tank with a flocculation chamber.Chemical coagulants are now used to dynamically change the condition of colloidal or suspended material and make them easier to remove via sedimentation. It is a well-established physicochemical technique for removing contaminants from textile wastewater samples Coagulants such as alum as well as iron salts are now used to improve the small particles that form agglomerates in wastewater. It creates a floc and produces a clean effluent free of suspended or colloidal particles. The amount of chemicals employed has an impact on the degree of clarity obtained.
Advantages
This method enhances the clarity of the water to eliminate sludge. The process of flocculation is used to purify the water, as well as sewage, and industrial wastewater. That’s why flocculants are commonly associated with wastewater treatment plants.
Limitations
Due to the obvious low dye removal efficiency as well as a large number of by-products sludge production, both flocculation and coagulation have their own set of limitations.
FILTRATION TECHNIQUE
Filtration techniques like microfiltration (MF), nano-filtration (NF), ultrafiltration (UF), and reverse osmosis (RO) are used to remove contaminants from textile effluents. The selection process for filter media in textile effluent treatment and their ability to consider the chemical content of textile wastewater is critical for removal processes. Membrane methods are used in textile factories to minimize BOD, COD, and color in discharge wastewater.
Advantages
Particles or substances are removed from liquids through filtration. This allows you to reuse oils, liquids, and coolants and protects machines and tools. It prevents the spread of contaminants.
Limitations
The initial investment, membrane clogging, wastes such as water-insoluble pigments, for instance, indigo dye, and starch applied decolonization membranes all have substantial drawbacks that necessitate further treatment.
SCREENING
Screening removes coarse floating debris like fabric bits, rags, fibres, lint, and yarns. The majority of the fibres are removed by screens and then by fine screens. Before the secondary biological treatment, residual fibres must be eliminated; alternatively, the secondary treatment system may be harmed. It’s been said that they clog trickling filtration, seals, and carbon beads. For screening we have the following screen types:
Coarse Screens
Coarse screens typically feature apertures measuring 6 mm and bigger, that remove heavy particles, rags, and trash from wastewater. Mechanically and physically maintained bar screens, as well as trash racks, are instances of coarse screens.
Fine Screens
Fine screens are commonly employed to eliminate particles that could cause difficulties in downstream processes, especially in systems that don’t have primary treatment. Fine screens typically have openings ranging from 1.5 – 6 mm.
Very Fine Screens
After coarse or fine screens, very fine screens with apertures of 0.2 to 1.5 mm can decrease suspended particles to values similar to those produced by primary clarifying.
Advantages
Physically cleaned screens need minimal to no maintenance operations and are an excellent choice for smaller operations with fewer screenings. Mechanically cleaned screens are less expensive to operate, and they provide better flow and screening capture.
Limitations
Manually cleaned screens need to be raked frequently to minimize clogging and excessive backwater levels, which cause a solids mat to form on the screen. The greater frequency of raking raises labour expenditures. During cleaning, removing this mat may generate flow spikes, reducing the solids-capture effectiveness of downstream units. Mechanically cleaned screens aren’t affected by this issue, although they require a lot of maintenance costs.
SEDIMENTATION
As Arsenic removal plants manufacturer sedimentation is a reliable and cost-effective way to remove suspended particles from textile effluent recycling system. This method is especially effective for the treatment of pollutants with a high proportion of configurable particles but when the debris is treated in conjunction with sewage. Lighter and smaller particles are deposited more easily in the sedimentation tanks due to gravity. Cross-flow sedimentation tanks, as well as center-feed circular filtrations, are the most frequent pieces of equipment utilized. Mechanical scraping and pumping out remove the settled sludge from sedimentation tanks.
Advantages
It’s a low-cost, easy-to-use water pre-treatment system. It is low-cost to operate and can address a variety of volumes. Coagulants shorten the time it takes to settle suspended particles. It has a highly efficient clarity and is compatible with sludge removal.
Limitations
The technique has drawbacks in that it requires more operations to set up the experiment, and convective disruptions in the density gradient occasionally occur, necessitating the process to be repeated.
EQUALIZATION
Untreated sewage streams have been trapped in a sump pit. Rotating agitators or pressurized air from underneath is often used to agitate blended effluents. The bottom of the pit is conical, which aids in the settlement of fine materials.
Advantages
The advantages of this system are pollutant level and consistent flow rate in the effluent discharged to treatment facilities.
Limitation
The system’s downside is its high construction cost, which is due to the huge number of basins necessary to keep entering wastewater streams one at a time.
NEUTRALIZATION
To remediate acid effluents containing metals in textile effluent treatment plants, neutralization can be utilized, which involves raising the pH of an acidic waste by adding an alkaline reagent, forming a precipitate, and extracting ppt. The pH of cotton completing effluents is typically upon this alkaline side. As a result, the pH of the equalized sewage must be adjusted. It’s not unusual to use dilute H2SO4 and CO2rich boiler flue gas.
Advantages
Whenever an acid and a base combine to generate salt and water, this is known as a neutralization reaction. These procedures will assist in bringing pH values closer to neutral. Soil can be more acidic at times. One instance is when decomposing pine needles influence the pH of the soil to drop.
Limitations
The water content is essential for acidic characteristics. Acidic or basic characteristics in non-aqueous solvents are not explained by the concept. It is unable to describe AgCl4’s acid content.
- SECONDARY TREATMENT The basic goal of secondary treatment is to reduce more BOD than can be removed by conventional sedimentation. It also eliminates a significant amount of phenol as well as oil. Secondary treatment removes or reduces dispersed and colloidal organic molecules, as well as color, from wastewater, and stabilizes organic debris. Bacteria and other microbes are used to accomplish this biologically. Biological treatment of textile effluents is possible [3]. These processes might be either aerobic or anaerobic. Bacteria and other microbes devour organic matter as sustenance in aerobic processes. They result in the following modifications in order:
- Flocculation and Coagulation of colloidal textile effluents (mainly colloidal matter)
- Oxidation of liquefied organic substance to CO2
- Nitrogenous organic matter’s degradation into ammonia and then into nitrite and later nitrate.
Sludge digestion is primarily accomplished through anaerobic treatment. The effectiveness of this process is determined by oxygen deficiency, temperature, pH, waste load, and the presence of harmful compounds. The following are some of the most often utilized biological treatment methods:
AERATED LAGOONS
Aerated lagoons are enormous storage tanks or ponds that are covered with cement, polythene, or rubber and have depths of 3-5 meters. The effluents from initial treatment operations are received in such tanks and aerated for 2 to 6 days using mechanical equipment like floating aerators. Throughout this period, a good flocculent sludge forms, causing the soluble organic matter to be oxidized. BOD elimination to the amount of 99 percent can be accomplished with effective running.
Advantages
Lagoon systems are designed and built at a low cost. They require less energy than the majority of wastewater treatment techniques. They’re relatively easy to operate, and they usually require part-time workers.
Limitation
The main drawbacks are the vast amount of space required as well as the microbial contamination of the lagoons, which demands additional biological treatment.
TRICKLING FILTERS
Trickling filters are circular or rectangular beds that are 1-3 m deep, created of well-graded media like PVC or gravel of 40-150 mm size. Wastewater is scattered homogeneously across the entire bed using a slowly rotating supplier fitted with orifices or nozzles. As a result, the wastewater seeps through the media. The filter is designed so that air could penetrate at the bottom, creating a natural draught that is counter-current towards the effluent flow. On the base of the filter media, a gelatinous layer of aerobic microorganisms and bacteria called Zooglea forms that flourish on the nutrients provided by the polluted water. During the transit of the wastewater, organic pollutants get deposited on the gelatinous sheet and then oxidized by bacteria and other microorganisms present.
Advantages
They are simple, efficient, and consume less electricity. A moderate amount of technical skill is required for system management.
Limitations
Operator monitoring is needed regularly. Moreover, additional treatment and problems like odour and vector are present.
ACTIVATED SLUDGE PROCESS
The most adaptable biological oxidation approach for the treatment of textile effluents comprising dissolved particles, colloids, and coarse particulate organic material is the activated sludge process. The contaminated water is aerated inside a reaction vessel whereby some microbial floc gets retained in this process. The aerobic bacteria degrade trash biologically generating water and carbon dioxide molecules while also utilizing organic materials for bacteria synthesis. Activated Sludge is formed when bacteria flora expands and laterals resist in the appearance of a floc. The discharge from the reaction vessel is filtered and evacuated after being removed from the sludge by settling. A portion of the waste is recycled into the same container to maintain a healthy microbial population for the next treatment process. The surplus sludge, combined with primary sludge obtained through primary sedimentation, is processed in a sludge digester. Industrial wastes require proper aeration over 5 to 24 hours. This technique is capable of removing BOD to the tune of 90-95 percent.
Advantages
The system itself is inexpensive to install and provides a fair financial return. As far as the effluent is of a consistent kind and quantity, as well as the activated sludge, remains active, the effluent water obtained is of excellent quality.
Limitations
This method isn’t particularly adaptable. It has negative impacts on the process’s operation when there is a sudden rise in the quantity of sewage or a quick transition in the composition of sewage. Consequently, poor-quality effluent is produced. The expense of operation is substantial.
OXIDATION DITCH
The oxidation ditch can be thought of as a variation on the traditional Activated Sludge process. After screening, wastewater is discharged further into the oxidation ditch. Mixed fluid including the sludge waste is pumped in the stream with the assistance of a motorized rotor. The hydraulic retention period is usually 12 to 24 hours for liquids and 20-to 30 days for solids. The majority of the sludge produced is recycled for use in the following treatment process. Excess sludge could be dried upon sand drying platforms without leaving a smell.
Advantages
A steady level of water and constant discharge minimize the weir overflow rate and remove the periodic effluent surge typical to other biological processes, it provides an extra measure of performance and reliability over all other biological treatments. Due to the longer bioactivity during the activated sludge process, it generates a lesser amount of sludge than in other biological treatment methods.
Limitations
In comparison to other variations of the activated sludge, the discharge suspended particles contents are rather high. This requires a larger land area. This might be expensive.
OXIDATION POND
The oxidation pond is a big deep pond in which bacteria and protozoa work together to stabilize organic materials in the trash. Algae in the pond give them the oxygen they need for their metabolism. For photosynthesis, the algae use the CO2 generated by the bacteria. Waste stabilization ponds are another name for oxidation ponds.
Advantages
The oxidation pond biological treatment is intuitive since it utilizes microbes and algae. In terms of installation, operation, and energy demands, this makes the treatment approach cost-effective.
Limitations
The management is fairly complicated. If not properly maintained, it might emit a bad odour and provide a mosquito threat during the process.
ANAEROBIC DIGESTION
Sludge is the liquid leftover from sedimentation tanks and compost tanks after anaerobic digestion. In a sludge digester, the contents of the sludge are slowly fermented or digested by anaerobic bacteria while the sludge is kept at a temperature of 35°C and a pH of 7-8 for around 30 days. The final products include CH4, CO2, and a small amount of NH3.
Advantages
It is an eminent and widely used procedure. It is flexible for processing both conventional and challenging wastes; and is a low-energy method, rendering it more eco-friendly.
Limitation
The cost of delivering oxygen to the microbes is the greatest drawback of aerobic digestion. Smaller plants, on the other hand, may not have as high an electricity cost for providing oxygen.
- TERTIARY TREATMENT
ADSORPTION TECHNIQUE
The adsorption technique has substantial appeal for its elevated removal of dyes out of contaminated water. The color mitigation procedure necessitates the selection of adsorbents due to their high binding, ability, and desorption fundamental features. Because of its large surface area and adsorption capability, commercially activated carbon is an effective adsorbent for removing colors.
Different researchers have used low-cost adsorbents such as zeolite, bentonite, ash, resins, and bentonite, for adsorption. Furthermore, for the removal of colors from textile effluent wastewater, numerous studies explored different biomass wastes utilized as an adsorbent, like wheat residue, modified ginger wastes, rice husk, etc. The research has been reported by different researchers utilizing low-cost adsorbent materials to remove the color from dye-containing wastewater. Some dyes and adsorbents are listed below
-
- Reactive Red-24 (RR-24) is removed using altered wheat residues (MWR) as an adsorbent.
- Using modified ginger waste, the crystal violet (CV) color is removed (MGW).
- To eliminate Reactive Orange 84, chemically activated from unfilled cotton flower agro-waste is used.
- Potato plant waste adsorbs dyes malachite green and methylene blue.
- Activated carbon with waste tea (ACWT) adsorbed acid blue 25 (AB25).
- Straw-based adsorbs methylene blue.
- Sugarcane Bagasse Ash adsorbs acid orange II.
- Capsicum annuum seeds adsorb Reactive Blue 49.
- Bagasse fly ash absorbs Methyl Violet dyes and Orange-G.
- Activated Prunus Dulcis absorbed Acid Green 25 dye.
- Clinoptilolite is used to remove the cationic dye.
- Activating natural bentonite is used to remove the Congo-red.
- Smectite-rich natural clays absorb anionic and cationic dyes.
Advantages
Adsorption has several advantages over other systems in that it is simple to construct and run. It works under mild operating conditions and over varied pH ranges. It produces no harmful by-products.
Limitations
The high cost and difficulties of recycling or desorption make it unsuitable for use. However, desorption, regeneration, expensive price, and dumping of the adsorbent have limited their usage. As a result, adsorbents can be utilized in adsorption methods with low initial pollutant concentrations or when adsorbents are inexpensive, readily available, and rapidly produced or desorbed.
ION EXCHANGE METHOD
The ion exchange technique is used to eliminate anions and cations from wastewater. Inside the ion exchange process, synthetic resins are commonly used. The ion exchange technique is widely used in softening hard water. However, it has only been used to remove dye from water. The benefit of this style is that no adsorbents are lost. It could be used to remove water-soluble colors. However, it is ineffective for water-insoluble pigments such as dispersion dyes.
Advantages
It is eco-friendly. It has a high flow rate of purified water. It requires little maintenance.
Limitation
Limited electrode life is the only disadvantage of this technique. Besides these advantages, ion exchange has some drawbacks, including calcium sulphides fouling, iron fouling, organic matter adsorption, organic contamination from the resin, microbial contamination, and chlorine spillages.
OXIDATION TECHNIQUE
To oxidize wastes, several oxidative compounds are used. Sodium hypochlorite quickly decolorizes pigment baths. But it is a cheap method, it releases a harmful chemical that is rapidly absorbed. When ozone decays, it provides oxygen and radicals, which react also with waste color chemicals, causing the hue to deteriorate. Arslan et al. examined the use of ionization and hydrogen peroxide in association with UV radiation to remediate textile dyes factory waste.
Advantages
They have rapid reaction rates. They have a small footprint area. They are non-hazardous and eco-friendly.
Limitations
The major disadvantage of these methods is that they require a good sludge-producing precondition. This method is so complex and expensive as well.
ELECTROLYTIC PRECIPITATION & FOAM BREAKDOWN
Exceptionally lengthy exposure durations were essential, electrochemical deposition of saturated color effluent by lowering in the cathode area of an electrolytic tank has been observed. Surface-active solutes accumulate at gas-liquid interactions, and foam separation is an investigative method based on this behavior.
Advantages
We can recover and recycle valuable metals by using efficient technologies. Organic matter separation is more successful and faster than conventional coagulation. This process is eco-friendly
Limitations
The gap between electrodes and the polarity between them affects the process. The conductivity also blocks the process. However, the costs of chemicals make this treatment approach incredibly expensive.
MEMBRANE BASES METHODS
Membrane processes comprise reverse osmosis and electrodialysis; methods
Reverse osmosis could be used to eliminate TDS from effluent. Reverse osmosis has high efficiency of up to > 90% for eliminating electrolytes and macroscopic species from dyestuff effluents. However, the major downsides of this procedure include dye fouling of the barrier after prolonged use and high maintenance costs.
Electrolytes, and also colors, are used in the dye bath. To reach optimal dye depletion, a basic electrolyte such as NaCl is required. In textile dyeing, for example, the Density in the dyeing pool is normally in the range of 25-30 g/l for strong tone and nearly 15 g/l for soft tone, although it can be as high as 50 g/l in exceptional conditions. In reactionary dyeing on a cloth, the exertion stage necessarily requires ample salt.
The ultrafiltration membrane technology in textile effluent recycling plants is suitable for reducing increased salt levels from wastewater so that it can be utilized in the production line. When electrolytes are available in the liquid waste, the hydrolyzed dye attraction (for responsive colouring on cotton) rises, making it more difficult to separate.

The soluble salts (ionic) can even be extracted using membrane technology by exerting an electrostatic attraction across the water, causing anions and cations to transport to their electrode surface via anionic and cationic porous barriers. Viscosity, suspended solids, crystalloids, and minor organics must all be eliminated before reverse osmosis.
Advantages
The process, like evaporation, is not constrained by equilibrium, allowing for the achievement of the required water and outflow concentration parameters. No equilibrium creates a separate limit.
Limitations
They require high energy and operation costs as well for working. They have a low flow rate and become a source of pollution when used continuously.
THERMAL EVAPORATION In the thermal evaporator, sodium persulfate has a larger oxidation tendency than NaOCl. In the research, oxidation decolorization of textile dyes by persulphate due to the generation of free radicals has been noted.
Advantage
The technique is ecologically friendly because no gunk is formed and no harmful chemical vapors are released during evaporation.
Limitations
They have high initial investment costs. They become a source of pollutants as well. Sensitivity to changing conditions and generates complex pollutants and chemicals
PHOTOCATALYTIC DEGRADATION
A sophisticated approach for decolorizing a broad range of dyes based on their molecular composition. When a photosensitive catalyst is exposed to Ultraviolet light, it involves high explosive radicals that can destroy molecules.
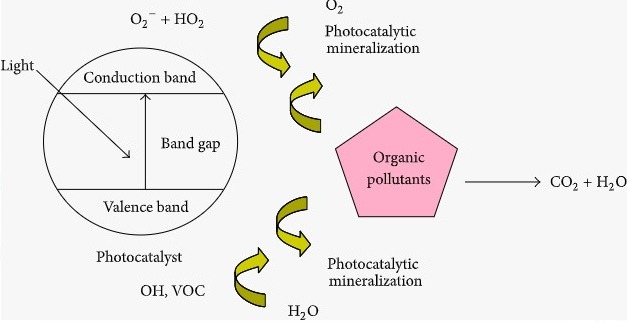
Advantages
This is a low-cost process. This is eco-friendly. This is reusable as we are using sunlight.
Limitations
The majority of semiconductor materials are either inactive or inactive in visible light. Separating the catalyst from the aqueous solution after photocatalysis is difficult.
ELECTROCHEMICAL PROCESS
They utilize less heat than most other non-electrochemical treatments of equal effectiveness, and no further reagents are necessary. It can also help to avoid the development of undesired by-products. However, if the wastewater treatment involves a significant quantity of floating or dispersion materials, the electrolytic process is hampered. As a result, before the oxidation process, those components must be properly eliminated.
Advantages
They are very effective at removing color from textile effluents. The reuse of discoloured waste is feasible, resulting in significant salt and water savings through the UVEC Cell.
Limitations
The electrolytic process can be inhibited by anode passivation and sludge accumulation on the electrodes in continuous operation. Post-treatment is required to eliminate high levels of ions from water.